The rapid evolution of the industrial landscape is fueled by the advent of Industry 4.0. This revolutionary paradigm seamlessly integrates cutting-edge technologies into manufacturing and diverse sectors. Central to this transformation is the proactive strategy of predictive maintenance, utilizing data and analytics to foresee equipment failures and prevent operational disruptions. Join us in this blog as we explore tangible industry 4.0 examples and delve into the realm of predictive maintenance, spanning across various sectors.
-
-
Industry 4.0 Examples: Automotive Industry Sector
-
Embracing the wave of Industry 4.0, the automotive sector has harnessed the power of predictive maintenance to optimize efficiency and minimize operational downtime. Production has evolved through smart manufacturing processes, with machines now communicating and adapting operations in real-time.
As we explore the realms of automotive smart manufacturing and predictive maintenance, it’s crucial to spotlight pivotal Industry 4.0 technologies that have taken center stage in this evolution.
- Additive Manufacturing: At the forefront of this transformation is additive manufacturing, a technology rapidly gaining momentum. Its impact on the automotive industry is multifaceted. Designers and engineers can now fabricate prototypes of products and components in significantly less time than conventional methods. This accelerated process expedites innovation and allows customization of automotive parts, once considered unattainable through traditional manufacturing. This technology is reshaping the industry landscape from 3D printing that empowers automakers to produce prototypes and replacement parts to establishing designated additive manufacturing centers by industry leaders like BMW and Volkswagen. Microfactories, an additive manufacturing product, are introducing a novel approach to vehicle production, emphasizing local manufacturing and agility.
- Predictive maintenance plays an equally pivotal role in the automotive sector’s evolution. The proactive approach of employing data and analytics to forecast equipment issues before they impede operations has revolutionized efficiency and minimized downtime.
This is where OCP Maintenance Solutions comes into play, offering cutting-edge predictive maintenance solutions designed to meet the specific demands of the automotive field.
Our advanced sensors and predictive analytics empower manufacturers to proactively detect potential equipment issues, strategically schedule maintenance tasks, and ensure the uninterrupted flow of the assembly line. Furthermore, our Vibox stands as a cornerstone in this transformative journey. By leveraging real-time data from the manufacturing floor, it anticipates maintenance needs, fine-tunes performance, and ultimately contributes to elevated product quality while curbing expenses.
For more in-depth exploration, delve into our comprehensive guide, “Predictive Maintenance in Automotive Manufacturing.” Here, we delve deeper into the profound implications of Industry 4.0 on the automotive landscape, shedding light on how predictive maintenance drives tangible progress.

-
-
Industry 4.0 Examples: Manufacturing Sector
-
Integrating the Internet of Things (IoT), data analytics, and automation through Industry 4.0 profoundly transforms manufacturing. This metamorphosis extends beyond predictive maintenance, encompassing various facets that revolutionize operational efficiency and efficacy.
- Routing Flexibility: In the quest for responsiveness, modern manufacturing demands adaptability. Fueled by IoT-enabled technologies, flexible manufacturing systems enable dynamic reactions to changing customer needs. Routing flexibility empowers manufacturers to handle equipment breakdowns seamlessly, ensuring uninterrupted production. Hierarchical models and dynamic simulations enhance factory adaptability, maximizing asset utilization and uptime.
- Machine Flexibility: As Industry 4.0 unfolds, manufacturing becomes more decentralized and autonomous. Driven by standard interfaces and intelligent infrastructure, machine flexibility paves the way for modular industrial networking and automation. ‘Plug and produce’ modules facilitate swift production line reconfigurations. This dynamic approach creates faster, intuitive maintenance, fostering more agile manufacturing lines.
- Remote Monitoring and Control: Manufacturing plants, often part of global networks, require comprehensive operational visibility. IoT-enabled architecture offers real-time insights from anywhere in the world. Remote monitoring empowers engineers to optimize individual asset performance. This approach identifies bottlenecks, reduces waste, and boosts overall equipment effectiveness. Varroc, a US automotive component manufacturer, achieved a 20% increased equipment effectiveness through this strategy.
- Predictive Maintenance: IoT and sensors enable real-time monitoring of industrial equipment. Machine learning-driven data analytics identify trends and anomalies, facilitating proactive failure pattern tracking. Predictive maintenance replaces traditional calendar-based approaches, preventing unplanned downtime and related costs. OCP Group, one of the world’s leading phosphate rock miners, phosphoric acid manufacturers, and fertilizer producers, employs this approach to detect and replace underperforming components before they fail.
OCP Maintenance Solutions is adeptly navigating this dynamic landscape, offering our IIoT Platform I-SENSE that empowers manufacturers with real-time insights into machine performance. This empowers informed decision-making for maintenance schedules. The I-SENSE software predicts potential issues and prescribes timely interventions by leveraging data from integrated sensors and historical records.
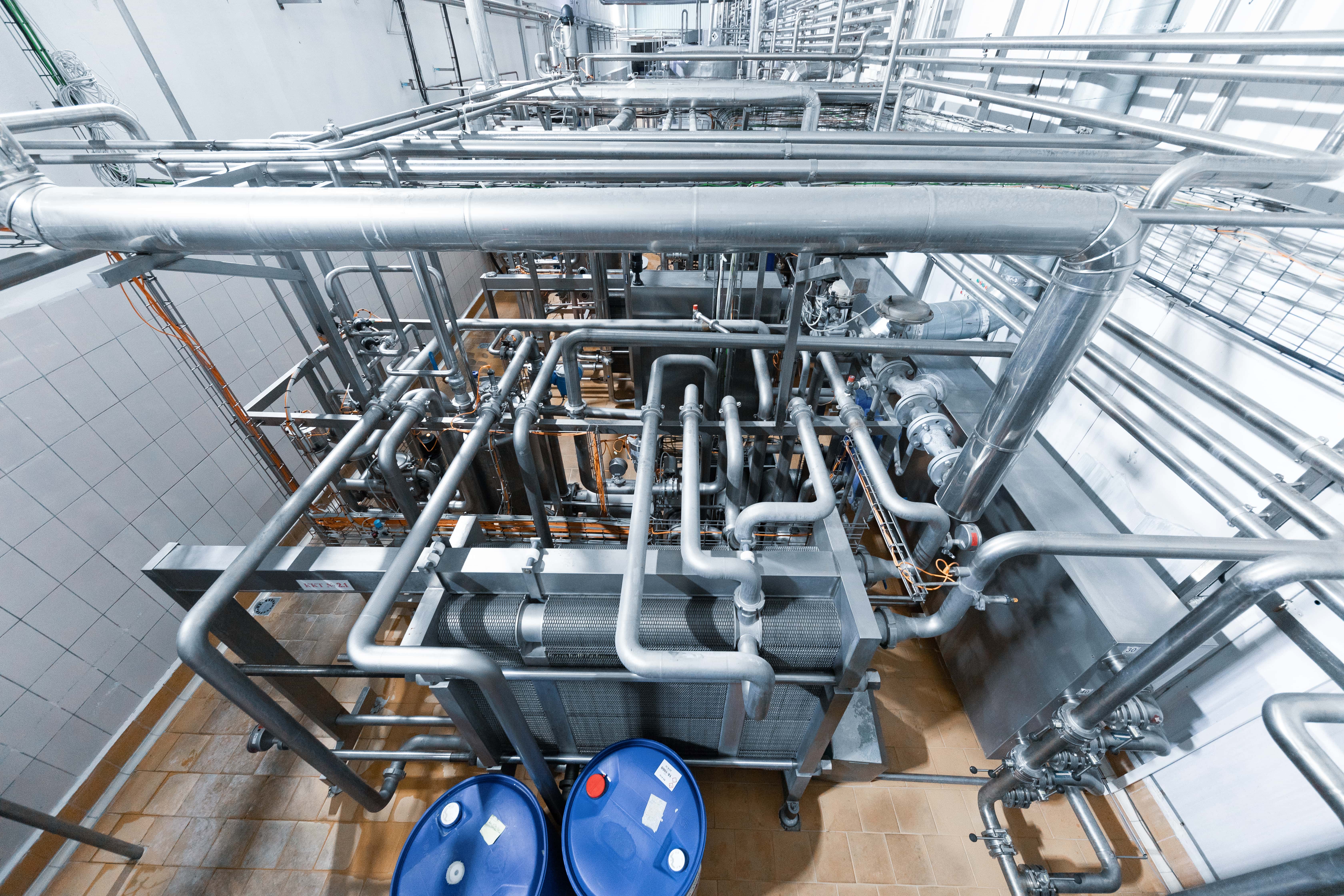
-
-
Industry 4.0 Examples: Energy and Utilities Sector
-
The energy and utilities sector is a testament to the formidable influence of Industry 4.0 and predictive maintenance. In an era of paramount efficiency and sustainability, these technologies have emerged as indispensable assets. As the demand for reliable energy supply grows, the sector has harnessed the potential of these advancements to fuel operational excellence.
Central to this transformation is the seamless interoperability of diverse assets, ranging from renewable generation to energy storage and adaptable loads — the embodiment of Energy 4.0 in action. This interoperability has paved the way for enhanced data-driven decision-making and optimization.
The application of data and monitoring within industrial sites has facilitated the identification of process inefficiencies and faulty equipment. However, rectifying this goes beyond simple equipment replacement; it encompasses integrating advanced software tools driven by artificial intelligence to optimize energy flows proactively. This concerted effort is potent, with the potential to reduce energy consumption across five industries by an impressive 13-29%, translating to a noteworthy 4% reduction in global CO2 emissions.
The digital revolution has bestowed numerous advantages upon the energy sector:
- Increased Energy Efficiency: The advent of smart grids, empowered by real-time energy usage detection and automatic adjustments, has led to substantial energy savings for consumers and utilities alike.
- Enhanced Customer Engagement: Digital technologies have fostered effective communication between utilities and customers, facilitating discussions about energy consumption, bills, and energy-saving avenues. This improved engagement cultivates satisfaction and loyalty.
- Improved Safety: Remote equipment monitoring and hazard detection have heightened the safety of both workers and consumers, proactively identifying potential risks.
- Reliable Energy Supply: Utilities have leveraged the digital revolution to predict and avert power outages through predictive maintenance, real-time monitoring, and advanced analytics.
Dive deeper into the impact of Industry 4.0 on the energy sector in our blog “Enhancing Energy Efficiency Through Industry 4.0” and discover how OCP Maintenance Solutions is driving the transformation.
Pages 171-188, ISSN 2096-2487,
https://doi.org/10.1016/j.ijis.2023.03.003.
(https://www.sciencedirect.com/science/article/pii/S2096248723000103)
-
-
Industry 4.0 Examples: Aviation and Aerospace Sector
-
Within the aviation and aerospace sector, the convergence of Industry 4.0 and predictive maintenance is propelling operations to new heights. In an industry where safety and efficiency are paramount, the fusion of these technologies stands as a game-changing force.
Pascal Brier, Executive Vice President of Strategy & Innovation at the Altran Group, underscores the pivotal changes ignited by Industry 4.0 in aircraft production:
- A Unique Data System (from the Silo to Cooperation): The conventional dissemination of aircraft production data across disparate systems is set for a revolutionary overhaul. Industry 4.0’s impact will bridge these information silos, creating a harmonious chain of data integration. Sensors will be strategically placed throughout this chain, transmitting real-time data on production status, stock management, and potential issues.
- New Digital Production Technologies: The fusion of Industry 4.0 introduces a new era of digital technologies. 3D modeling and additive manufacturing are poised to transform part design, making them lighter, smaller, and more cost-effective. This, in turn, transforms production lines, rendering them more flexible and responsive.
- A Centralized Control Room: The proliferation of smart, interconnected machines necessitates the creation of centralized control rooms. These hubs collate data from various machines and production sites, offering real-time visibility and aiding operators in their tasks. This
- Interaction Between Man and Machines: Industry 4.0 heralds the era of automation, with collaborative robots or “cobots” sharing tasks between humans and machines. This alliance significantly boosts productivity and safety, with McKinsey estimating a 75% increase in unit productivity per post.
Explore further insights into the impact of Industry 4.0 on aerospace manufacturing in our comprehensive blog, “The Impact of Industry 4.0 on Aerospace Manufacturing.”
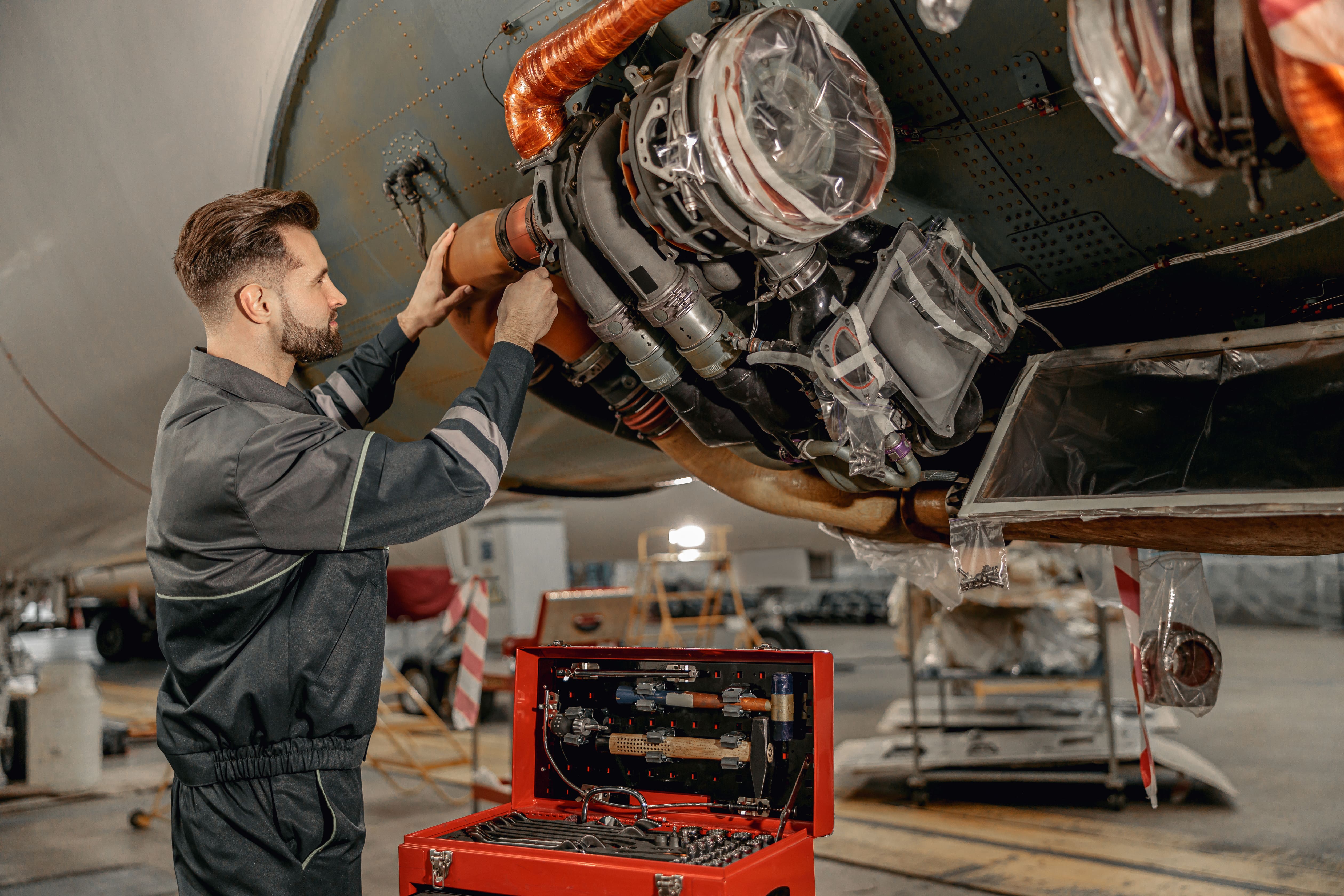
-
-
Challenges and Implementation
-
Integrating Industry 4.0 and predictive maintenance brings forth various challenges that must be navigated strategically. These advancements demand the expertise of skilled professionals, robust data management practices, and effective change management strategies. As you embark on this transformative journey, OCP Maintenance Solutions is your steadfast partner, providing comprehensive support at every juncture.
The pursuit of Industry 4.0’s transformative potential is not without its obstacles. Recent research has identified five common barriers that organizations may encounter in their digital transformation efforts:
1. Lack of Skills or Talent: The intricate structures of Industry 4.0 often necessitate specialized skills, which might be scarce in the workforce. Finding, training, and re-skilling staff in user interface, data science, software development, and machine-level controls can be challenging.
2. Data and IT Security: The heightened connectivity in Industry 4.0 raises concerns about IT security. Online integration of processes and systems can create vulnerabilities, including cyber attacks, network misconfigurations, and device failures, which can disrupt operations.
3. New Business Models: Digital technologies introduce new business models, requiring organizations to reassess their strategies. Aligning internal perspectives on these strategies can be a hurdle, especially without a consensus or the right people to drive the change.
4. Culture Change: The success of Industry 4.0 hinges on managing culture change effectively. If employees are unprepared for technological shifts, resistance and lack of adaptation can hinder progress. Leadership and change management play vital roles in overcoming this challenge.
5. Capital Investment: While Industry 4.0 offers substantial benefits, its adoption might entail significant upfront costs. However, sizable investments are not always necessary. Starting small and scaling gradually can provide insights into feasibility and effectiveness without committing to a massive expenditure.
As your dedicated partner in this journey, OCP Maintenance Solutions is equipped to address these challenges head-on. Our expertise extends beyond solutions to encompass comprehensive support for implementation, skills enhancement, and strategic change management.
For an in-depth exploration of conquering the hurdles accompanying Industry 4.0 adoption, we invite you to delve into our enlightening blog, “Overcoming Challenges in Adopting Industry 4.0.” Here, we share valuable insights and strategies to ensure a seamless and successful transition into the era of Industry 4.0, where possibilities are limitless, and OCP Maintenance Solutions is your guiding light.
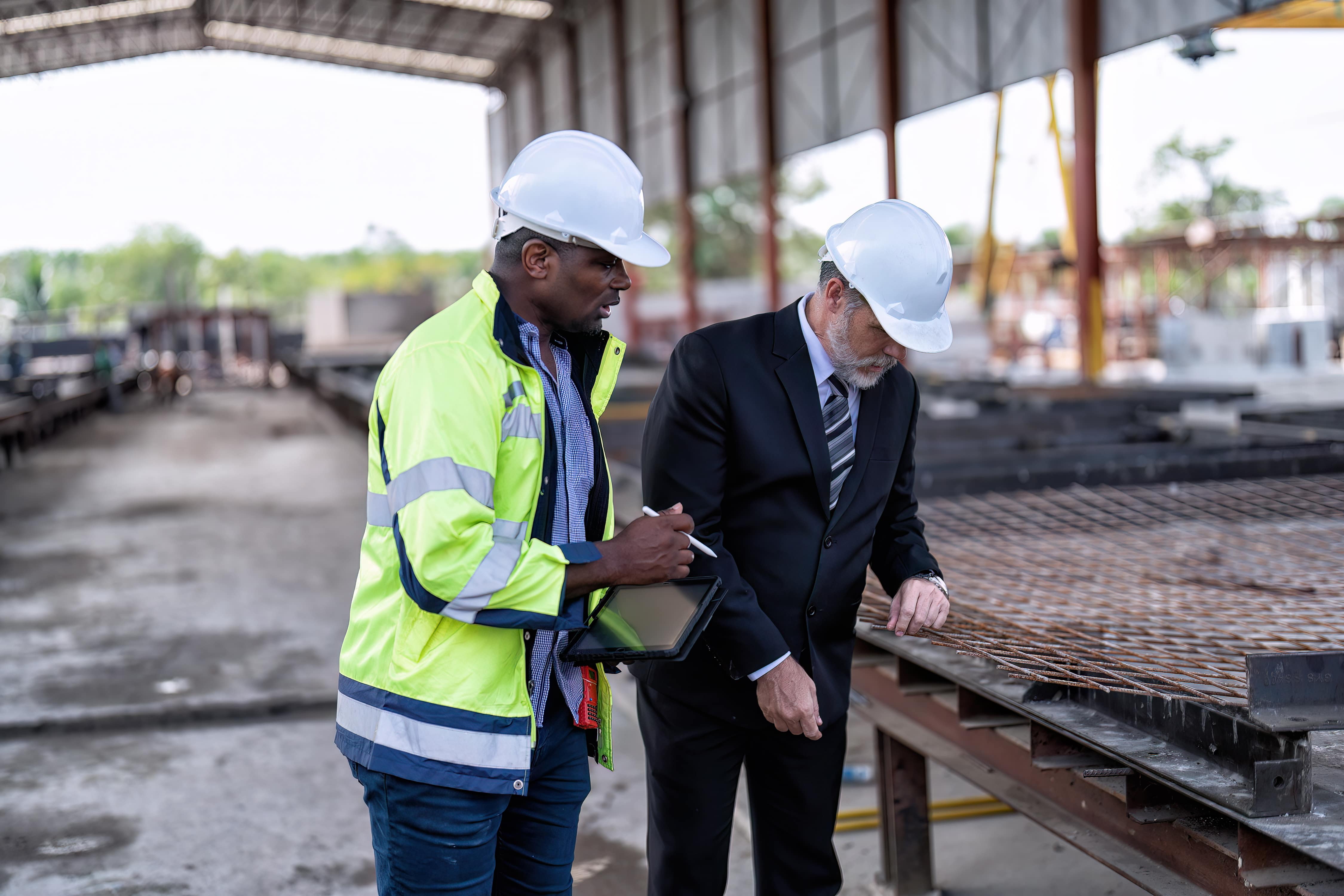
-
-
Conclusion
-
The era of Industry 4.0 has ushered in a transformative wave across industries, redefining how we approach manufacturing and operational efficiency. As you’ve journeyed through this exploration of Industrial Revolution 4.0 and predictive maintenance, you’ve witnessed how advanced technologies are reshaping the automotive, manufacturing, energy, and aerospace sectors.
At OCP Maintenance Solutions, we’re committed to propelling your organization amidst this dynamic landscape. Our advanced sensors, predictive analytics, and revolutionary I-SENSE software empower you to anticipate potential equipment issues, strategically plan maintenance tasks, and elevate product quality while managing costs.
As you contemplate embarking on your Industry 4.0 journey, it’s essential to acknowledge and overcome the challenges. From skills acquisition and IT security to culture change and capital investment, we’re prepared to stand beside you every step, providing comprehensive support and tailored solutions.
Your next step is simple – reach out to us. To embark on this transformative journey, embrace the potential of Industry 4.0, and drive your organization to new heights, visit our Contact Us page. Let’s embark on this journey together and harness the power of Industry 4.0 to unlock unprecedented efficiency, productivity, and innovation.
➡️ Ready to embrace the future with Industry 4.0, Maintenance 4.0, and predictive maintenance? Explore our range of products and services tailored to your industry’s needs. Connect with us through our “Contact Us” page to learn how OCP Maintenance Solutions can elevate your operations and drive efficiency in this era of technological advancement.