
Enhance Efficiency and Accuracy with Inspection 4.0


Uncover Hidden Insights with Data-Driven Inspection Solutions

What is Maintenance Inspection?
Maintenance inspection is an integral part of any industrial maintenance program. It encompasses tasks to assess equipment conditions and identify necessary resources for servicing.
Maintenance inspections involve evaluating the state of machines and equipment. These inspections aid in discerning the essential tools, materials, and labor necessary to sustain optimal operational functionality.
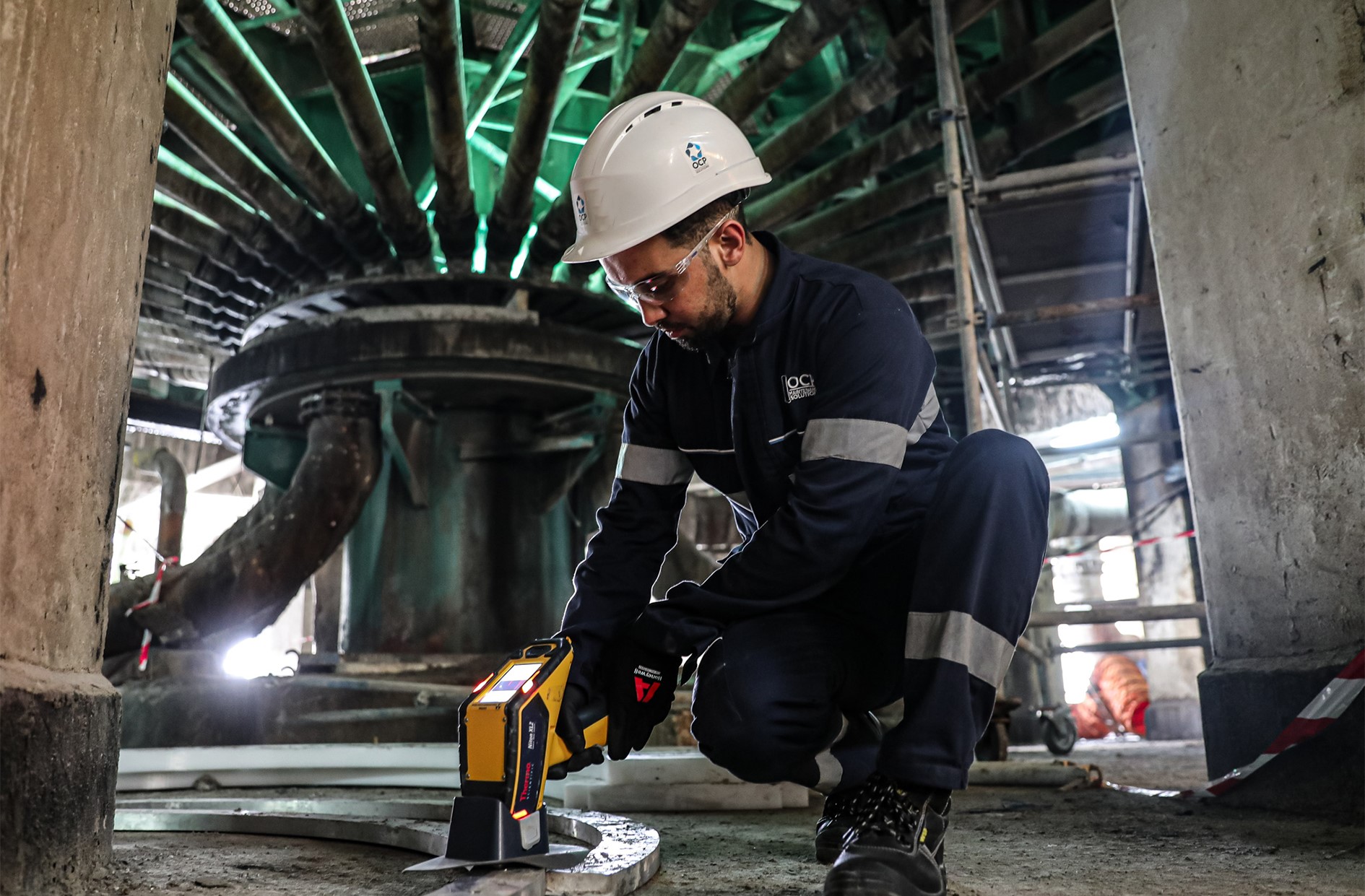

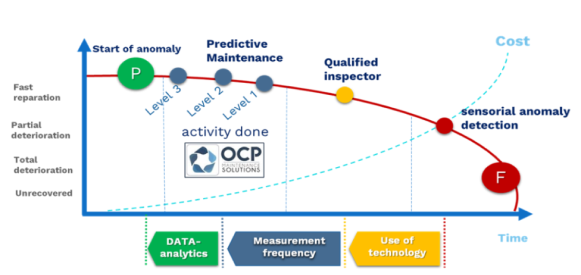
Why It is Important
Human-based inspection is no longer viable. Not only is the workforce diminishing in nations like Europe and Japan that are rapidly aging, but companies must contend with more significant human expenditures, more frequent training costs, and quicker employee turnover due to a smaller labor force.
Additionally, Inspection 4.0 leverage technology to detect anomalies before any human can. There are instances when quality inspection becomes a question of subjective opinion, even in businesses with clearly stated quality standards. This is why Inspection 4.0 means improving and automating inspection workflows to follow faster and more efficient production processes and improve them.
Our Solutions
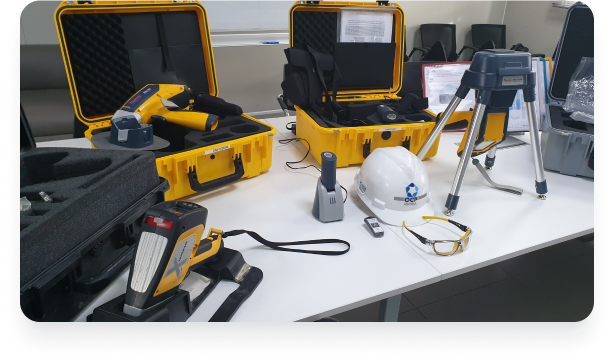
NDT and Corrective Actions
NDT or Non-Destructive Testing is a set of techniques that do not damage industrial equipment when inspected, producing reliable results quickly for preventive or corrective measures. NDT techniques are used in industrial plants to inspect cast and forged components, pole and pipe systems, and plant, vessel, and pipeline construction components.

Condition Monitoring
Condition monitoring (CM) is the mechanism by which monitoring a specific parameter in a machine condition (such as temperature, vibration, …) takes place to spot any changes that might indicate an increased risk of failure. Implementing condition monitoring is critical to predictive maintenance since it enables maintenance scheduling and preventative measures to prevent additional loss and ensuing unexpected downtime.
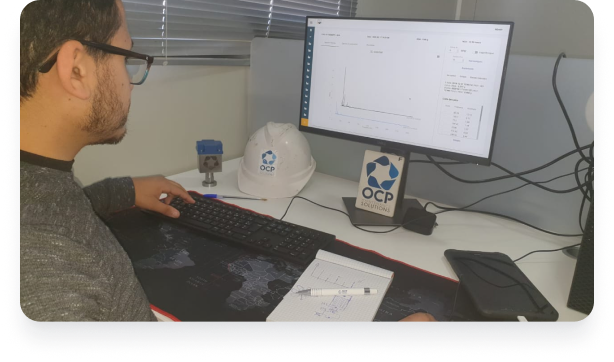

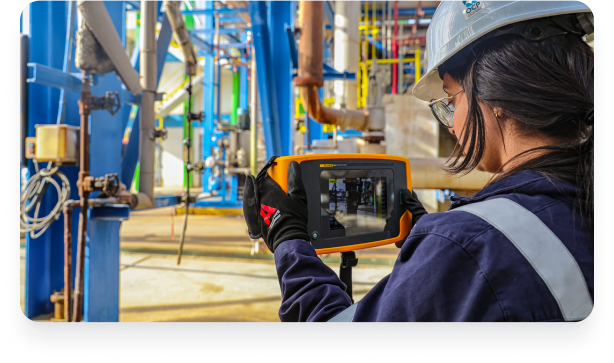
Energy Efficiency
Among the steps to improve energy efficiency, we have the detection of compressed air and steam leaks, which are among the leading causes of energy loss, which implies the importance of hunting and eliminating them.
Thanks to the latest technological advances in acoustic imaging, detecting these leaks has become simple and fast.

Lubrication
Equipped with a state-of-the-art oil analysis laboratory, OCP Maintenance solutions offers to monitor your oils regularly through the analysis of samples taken from your equipment and detecting most defects in lubricants related to gears, pumps, compressors, turbines, engines, hydraulics, machines, and processes, …*
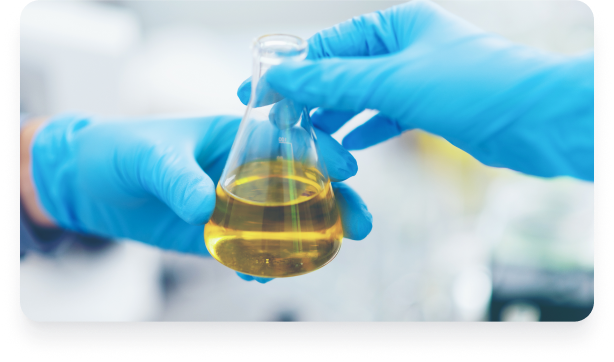
