

Non Destructive Testing




OCP MS' Expertise In Non Destructive Testing.
Non destructive testing (NDT) is at the core of our services, safeguarding the reliability of your industrial assets. Our expertise ensures product and machinery security, from materials testing to welding quality.
Recognizing industry’s need for efficiency, our Total Quality Assurance services cover an array of areas including production, compliance, maintenance, and more. We assure swift turnarounds, keeping your operations seamless.
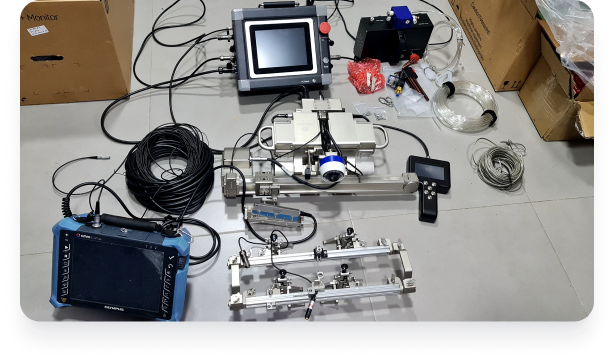
Our History In Non Destructive Testing.
Our extensive proficiency includes working closely with one of the leading global phosphate producer, which has equipped us with unparalleled insights. This experience empowers us to employ the most suitable techniques and methodologies for identifying flaws and anomalies in your products, equipment, production facilities, or industrial assets. The data we provide aids you in making well-informed decisions. By leveraging our expertise, you can proactively address issues before they escalate, mitigating the potential for significant consequences, financial setbacks, and operational inefficiencies.
Several different NDT techniques can be used, including:
- Visual inspection: Ultrasonic testing: (PAUT, TOFD)
- Magnetic particle inspection
- Liquid penetrant testing
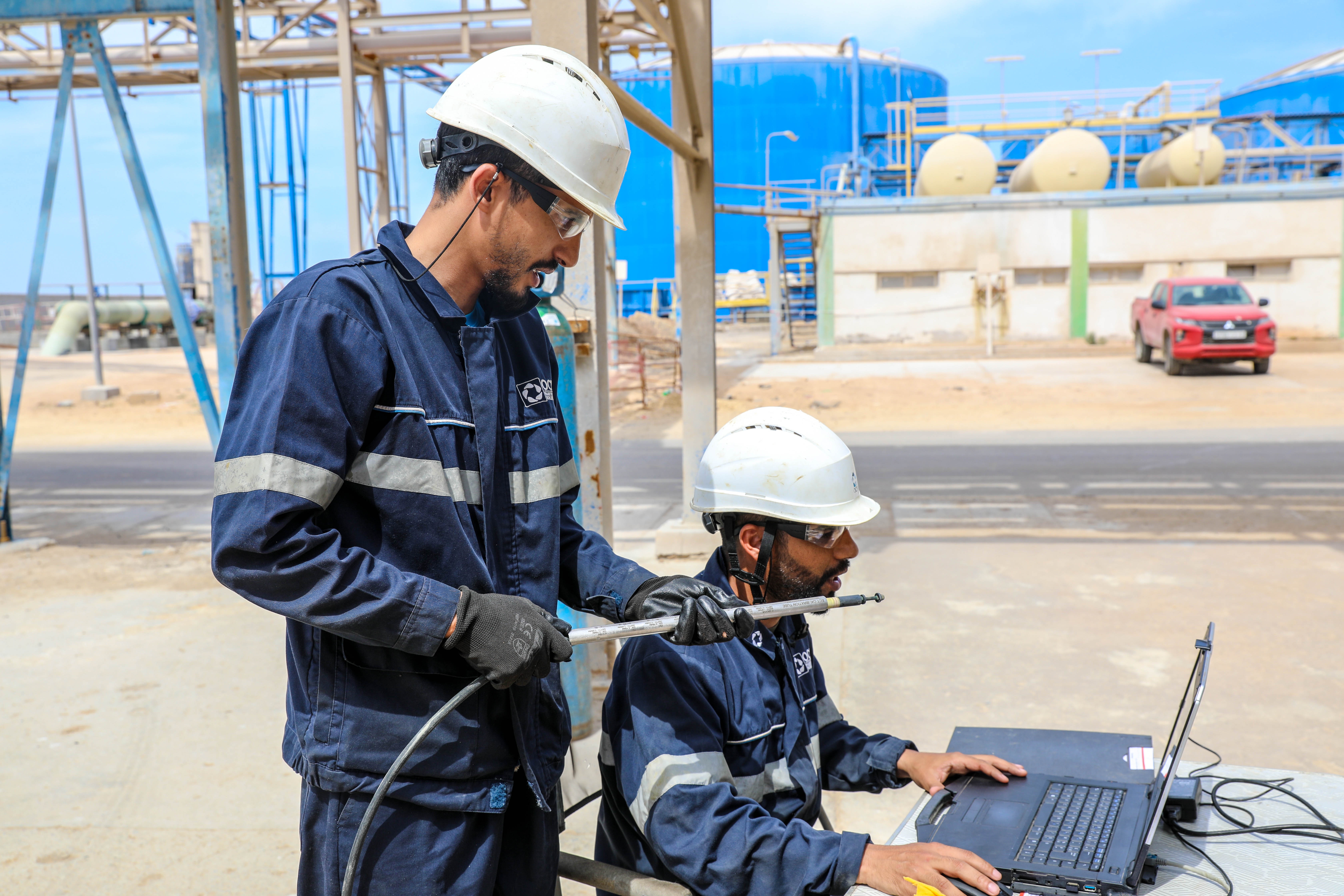
Why Use Non Destructive Testing in Your Maintenance?
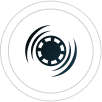
Non-destructive testing provides a critical layer of safety assurance by detecting flaws, defects, or material degradation in assets without causing damage.
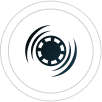
By assessing the structural integrity and performance of equipment, NDT helps detect hidden defects or weaknesses that could lead to catastrophic failures.
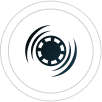
By evaluating the internal and surface conditions of components, NDT verifies the integrity and quality of materials, welds, and structures. This helps in meeting regulatory requirements, achieving compliance, and extending the lifespan of assets, reducing the risk of unexpected failures.
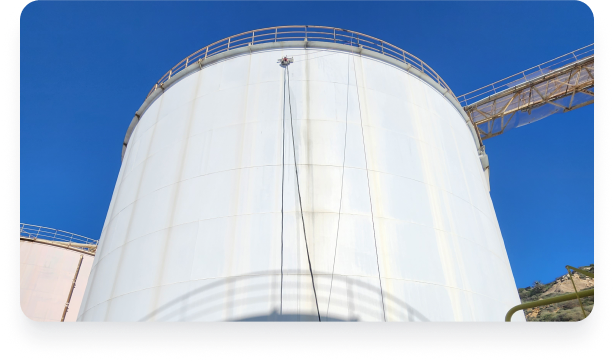
Corrosion Mapping
Ultrasonic corrosion mapping is a non-destructive technique that uses ultrasonics to map the thickness of a material. Corrosion-related variations in material thickness can be located and graphically represented as an understandable image.
A high likelihood of finding corrosion defects like pitting and the assurance that the entire region of interest has been covered lead to a successful corrosion mapping inspection. These technologies increase the lateral resolution to surface scan speed ratio and make two-axis scanners more readily available.

Eddy Current Inspection
Eddy’s current inspections can be divided into two parts. ECT and RFT:
- ECT: Eddy Current Testing is one of the non-destructive testing techniques that use the electromagnetism principle to find flaws in conductive materials is eddy current testing. The test surface is positioned close to a specially made coil powered with an alternating current, creating a shifting magnetic field that interacts with the test portion and causes eddy currents nearby.
Then, changes to the alternating current flowing in the primary excitation coil are monitored, with variations in the changing phases and amplitude of these eddy currents, either with the aid of a receiver coil or by taking measurements of the changes in electrical conductivity and the test part’s magnetic permeability - RFT: Finding flaws in steel pipes and tubes is the primary use of the non-destructive testing technique known as remote field testing (RFT), which uses low-frequency AC. Eddy current testing in the remote field is another name for RFT (RFEC or RFET). Although a magnetic field is utilized rather than electromagnetic, RFET has occasionally been used as a distant field electromagnetic technology. When an RFT probe is moved down a pipe, it can detect flaws inside and outside with roughly similar sensitivity (although it can not discriminate between the two). Even though non-ferromagnetic materials like copper and brass can be used with RFT.
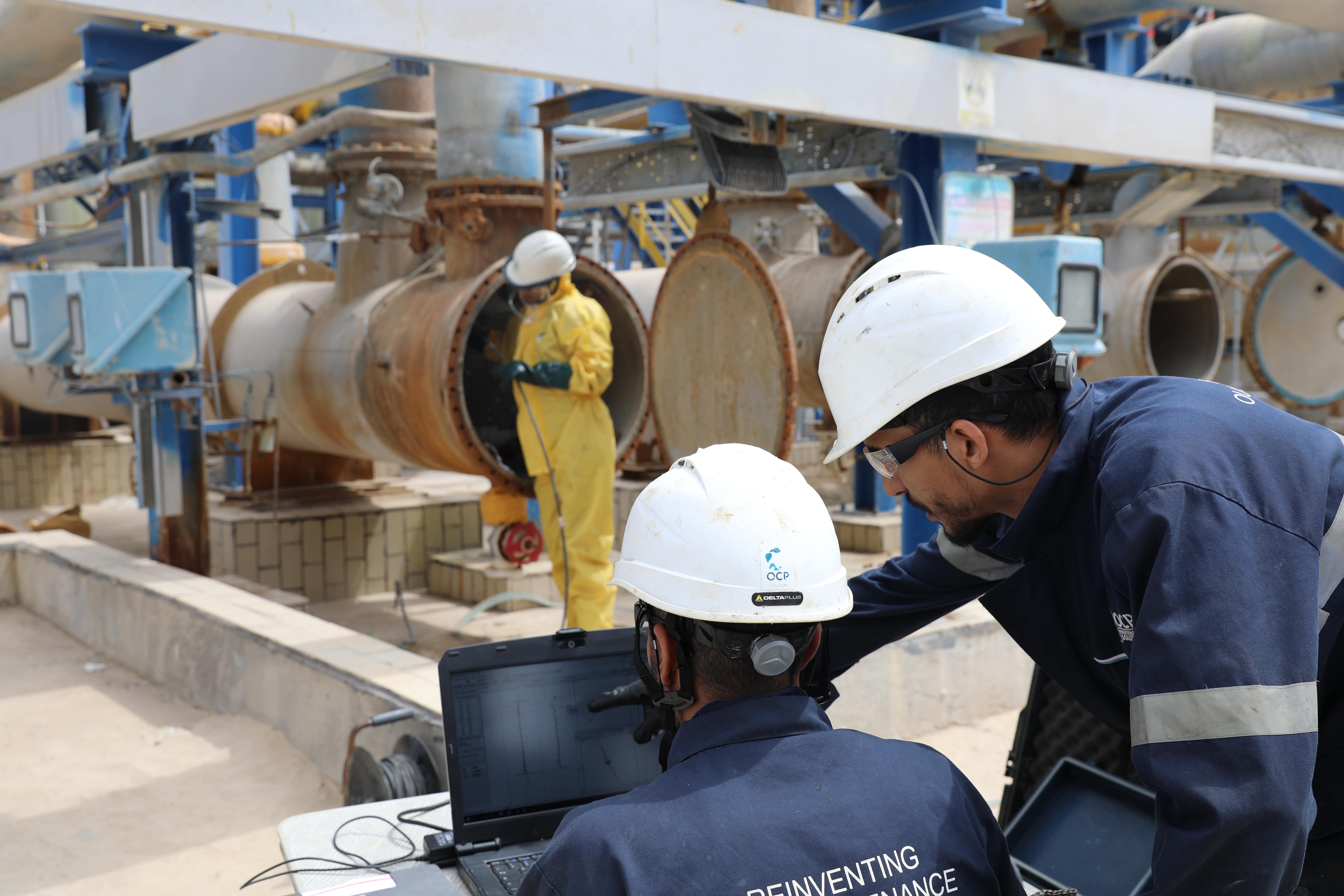

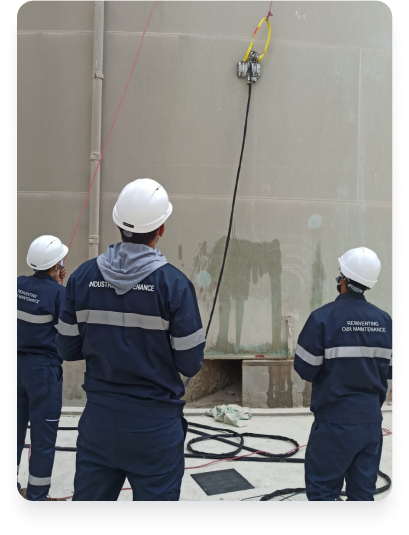
Robot Thickness Measurements
Robotic thickness measurement is a process in which a robot accurately measures the thickness of a material or component.
This is typically done using specialized sensors or probes mounted on the robot and designed to measure the thickness of the material at multiple points.
There are several benefits to using a robot for thickness measurement. For one, robots can accurately and consistently measure the thickness of a material, even if the surface is irregular or difficult to access.
Additionally, robots can work faster and more efficiently than humans, reducing the overall time and cost of the thickness measurement process.
Robotic thickness measurement is commonly used in industries such as manufacturing, aerospace, and automotive, where it is essential to accurately measure the thickness of materials to ensure the quality and reliability of products. It is also used in industries such as oil and gas, where it is necessary to measure the thickness of pipes and other components to ensure their structural integrity.

Frequently Asked Questions (FAQs)
Yes, we can provide you with a detailed and mapped graphic of the integrity of the tubes on your boiler, exchangers, and condenser….
Yes, we have a scanner that can perform color mapping, and welding inspection using phased array + TOFD
Yes, we have a scanner that can perform color mapping, and welding inspection using phased array + TOFD
Get in Touch with One of Our Experts
We will get back to you in under 48 hours
*by clicking the “Submit” button, you agree to provide us your personal details and confirm you have read and agreed to our Privacy Policy.