

Online Condition Monitoring Systems




What is Online Condition Monitoring Systems?
Online condition monitoring systems are a process that involves continuously collecting and analyzing data from industrial equipment and systems to detect and diagnose potential problems and failures before they occur.
Online condition monitoring aims to improve industrial equipment and systems’ reliability, availability, and efficiency by identifying and addressing issues before they cause unexpected downtime or other disruptions. Online condition monitoring is typically accomplished using sensors and monitoring systems that continuously collect data on various parameters, such as temperature, vibration, pressure, and flow. The data is then analyzed using a combination of software algorithms, predictive analytics techniques, and human expertise to identify patterns and trends that may indicate potential problems.
This information can trigger alerts or notifications or initiate preventive maintenance actions to address potential issues before they become more serious.
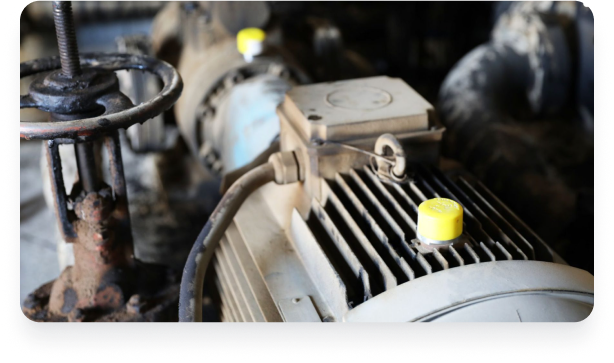

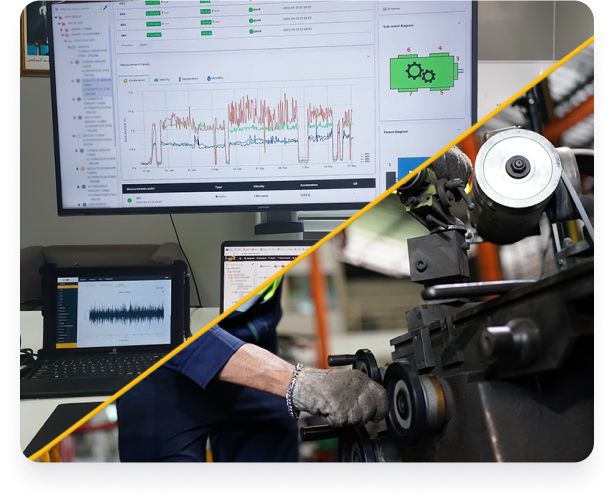
Classic vs Online Condition Monitoring Systems
Traditional and online condition monitoring are both methods of detecting and diagnosing potential problems and failures in industrial equipment and systems. However, there are some critical differences between the two:
- Frequency of data collection: Online condition monitoring involves continuously collecting data from the equipment or system in real-time, while traditionally, it must be done manually.
- Data analysis: Online condition monitoring often involves using software such as I-Sense and predictive analytics techniques to analyze data automatically and identify patterns and trends that may indicate potential problems, while traditionally, it involves manually analyzing data and identifying potential issues based on knowledge and experience.
- Response time: Traditional condition monitoring relies on scheduled inspections or maintenance tasks to address potential problems, which may not be timely enough to prevent unexpected downtime or other disruptions. Online condition monitoring can provide almost immediate notification of potential problems, allowing maintenance teams to take timely action to address them.

Our Product Line
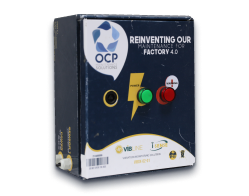
Vibox
A condition monitoring system that protects your machines from damage and improves the efficiency of your assets.
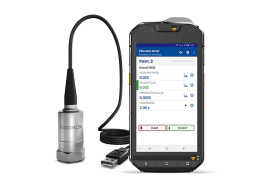
Mobivib
A mobile data acquisition kit that enables on-the-spot vibration measurement and spectrum analysis for industrial assets.
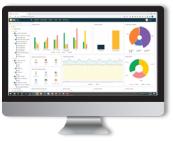
I-SENSE
A highly scalable, IoT platform that allows devices to connect and exchange information in real-time securely.
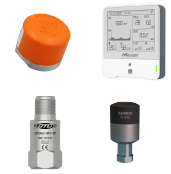
Sensors Store
From temperature sensors to motion and proximity sensors, we offer reliable and high-quality solutions to meet your needs.
What Are the Most Reccuring Machine Faults Detected by Our Online Condition Monitoring Systems?
These are just some of the multiple faults detected by our solution. For more information, please refer to the use cases where you can find further details.
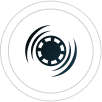
A misalignment results from 2 shafts not being parallel to each other, which can result in high vibration levels and premature asset wear. Luckily with online condition monitoring, you can detect it and act on it before failure.
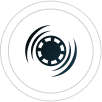
An imbalance happens when the rotor center of mass does not coincide with its center of rotation, causing a centrifugal force that can be detected with our vibration analysis system.
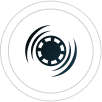
Bearings have 4 elements (inner ring, rolling elements, cage, outer ring) in constant contact, because of the continuous rolling and poor lubrification quality, metallic particles disintegrate, causing high vibration levels depending on the severity of the wear. But thanks to Vibox, we can detect those anomalies early at the initial wear states.
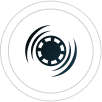
They are the most complicated type of failures to address because levels can vary from one gear to another, to be able to analyze and detect gear failures more advanced algorithms are used to detect the presence of impacts and to qualify the severity of the failure. Our online monitoring systems give you the possibility to monitor the evolution of the degradation of the gear.
Get in Touch with One of Our Experts
We will get back to you in under 48 hours
*by clicking the “Submit” button, you agree to provide us your personal details and confirm you have read and agreed to our Privacy Policy.